Natural Materials exhibition at 85 Southwark Street
As a practice, we strive to design beautiful buildings with long lifespans that can adapt over generations. Sometimes, this approach involves experimenting with new methods of construction and unorthodox materials. While the use of stone in construction is often perceived as traditional material, primarily for heritage projects, we believe that it is an exciting area of research in contemporary building practice - with great potential for innovation.
In the Spring of 2024, we were asked by Arup, a multinational engineering firm, to envision the facade of the future. With buildings responsible for 39% of global energy-related carbon emissions and façades contributing up to 31% of a building's embodied carbon, this design challenge is crucial for sustainability.
When situated close to public transportation, local amenities and employment opportunities, compact and tall development can offer environmental, social and economic benefits. Yet, tall buildings face unique design challenges due to increasing performance requirements and, in turn, greater façade complexity. Their height complicates access for construction and maintenance, making these processes costly.
Reinforced concrete "doughnut" panels can mitigate these issues. Their simple precast construction allows for safe and efficient installation, using relatively few components. Well-designed inter-panel joints mimic durable masonry walls, which can last for centuries, allowing for easy access for window replacement and other infill components. However, reinforced concrete often carries high embodied carbon costs.
Stone, an ancient, contextual, and low-carbon material, has the potential to define a more sustainable future. Many proposals are being developed for load-bearing stone façades, maximising stone’s durability and compressive strength. However, these façades are less practical for tall buildings due to construction challenges and thick structural elements needed to manage concentrated loads.
To combine the benefits of stone with doughnut panels, we propose the Stonut: a low-carbon, pre-manufactured, durable stone doughnut panel. The Stonut consists of small stone pieces held in compression by durable tendons. Smaller dimensions facilitate automated manufacturing, expand usable stone options, and allow profiles to adapt to varying loads. Different types of stone can be used for sides and spans, while cornerstones manage complex loads. Glazed and solid infill panels can be accessed from the interior for maintenance or replacement, allowing adaptability over time.
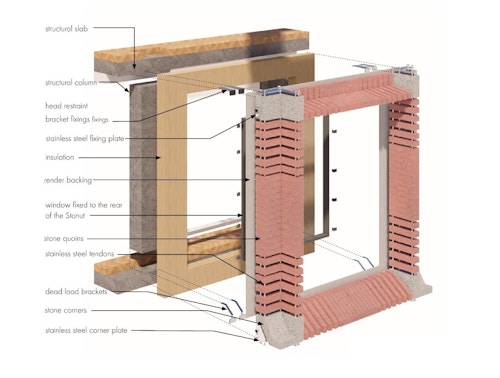
The Stonut panel
The Stonut’s perimeter is formed by tendons pulling the corners together, enabling the stone to act in compression. Dead and live loads are directed to the corners, where brackets transfer them to the building structure. Higher stresses at the lower corners are managed with stainless steel plates. Brackets, like the Stonut, are designed to minimise volume and thermal bridging, reducing upfront carbon.
Stones can be profiled for optimal function based on their location on the Stonut. For example, 'L'-shaped stones can serve as mullions, while other shapes provide solar shading or weathering benefits. Nesting techniques and CNC cutting optimise material use and minimise waste.

Stones can be tailored to local materials; dense igneous rock may be used for concentrated stresses at corners, while other geologies suit different facade areas. Lime putty can bed the stones for weather tightness, supported by a waterproof render for additional protection.
In many respects, the Stonut functions similarly to the concrete doughnut: windows, louvres, solar shading, and spandrel panels can be integrated, while insulation and dry linings can be added on the interior. This design allows for future maintenance and upgrades without complex high-rise access.
Although it requires further research and development to improve resistance to moisture ingress, thermal bridging and the monetary and carbon costs of the stainless steel components, the Stonut has the potential to offer a simpler, safer, more circular and adaptable building module for sustainable construction.

This article originally appeared in Issue 2 of Natural Stone Journal.